Eiffage VSE, a subsidiary of the 6th largest European construction group.
Eiffage VSE specializes in the assembly, refurbishing, customization and maintenance of electromechanical installations. Subsidiary of the sixth construction group in Europe, Eiffage VSE is active in Belgium via its facilities in Aalter and Brussels. The company’s 220 employees work in various sectors such as waterways, subways, tunnels, roads and airports. In order to meet its customers’ expectations, VSE now offers a CMMS solution: CARL Source Factory, to manage the tunnels in the Belgian capital and the traffic lights in the Brussels region.
Digitizing the maintenance process
For Eiffage VSE, the digitization of maintenance processes gives a strategic advantage. It meets the objectives of optimizing the company’s activities, as well as the requirements of its customers, who demand that their contractual maintenance be managed by CMMS.
In 2015, Eiffage VSE chose the CARL Source solution. Its benefits: Ease of use for technicians and customers, extensive customization, and a wide array of features allowing users to manage all processes, from preventive maintenance to invoicing. The project begins with management of the lighting system in the Brussels tunnels, before extending to the traffic lights in the region.
« …carry out curative maintenance operations 24 hours a day, 7 days a week within a one-hour turn. »
Benoit De Wailly, Roads and Airports Regional Manager – VSE Eiffage
Eiffage VSE: a project to improve the efficiency of technicians
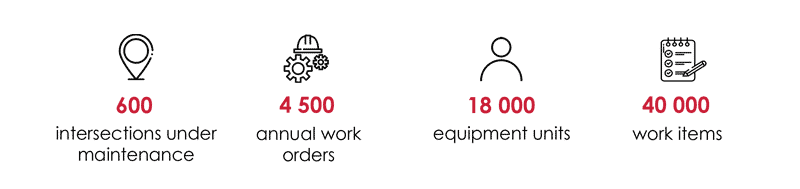
Deployment of CARL Source Factory equipment maintenance software
The CARL Source Factory software, already in place for lighting management in the Brussels tunnels, is deployed by the department in charge of maintenance of the Brussels traffic lights. The scope is extensive, the goal being to install, renew and maintain more than 600 intersections, which must be 100% operational at all times. The project team relies on the extensive customization capabilities of the software to adapt the solution to different user profiles. Intersection data is imported into the CMMS via the CARL Loader module, i.e. 40,000 work items and several preventive maintenance ranges.
For the project team, it is important to simplify as much as possible the use of the software and the work order process, from its creation in the system to its completion by the technician. Hence, the customer’s request sent by email in PDF format is automatically saved in the CMMS system, triggers a work order, which is assigned to a technician according to his/her availability and the nature of the work.
On the technician side, the process is simple; the technician receives notification of the service call, with all the relevant technical details, on his/her Mobile CARL Touch CMMS tool – which works with or without a network – along with a copy of the PDF file and closes his/her service call with a custom report.
« The traceability of operations makes it possible contractually to avoid any arguments on service call deadlines. »
Benoit De Wailly, Roads and Airports Regional Manager – VSE Eiffage
Results on maintenance interventions
Maintenance work – Eiffage VSE
With the CARL Source Factory solution, Eiffage VSE is able to centralize and log all work orders on the 18,000 equipment units to be maintained. This results in significant time savings for technicians, who improve their efficiency by viewing the equipment history via CARL Touch. “With their mobile CMMS tool, technicians are more efficient; they have a very clear view of the status of each piece of equipment, which prevents them from having to start over or repeat what has already been done in terms of troubleshooting,” declares Benoit De Wailly, Roads and Airports Regional Manager.
Traffic light intersections require verification once or twice a year, which adds up to more than 1,000 annual preventive maintenance operations. The settings of the CARL Source solution now make it possible to “carry out curative maintenance operations 24 hours a day, 7 days a week within a one-hour turnaround,” confirms Benoit De Wailly.
Optimize maintenance management.
The Roads and Airports Regional Manager continues, “the traceability allowed by CARL Source makes it possible to clarify all arguments regarding service call deadlines and thus avoid any contractual penalty”. The 25 users can insert a large number of photographic images into the software to verify the proper execution of the work, and the customer is kept informed over time of the status of their equipment, being notified at the end of each service call. BIRT reports and performance metrics are also generated via CARL Source Factory in order to analyze the 4,500 annual service calls and optimize maintenance management.
Our equipment maintenance solution for the industrial sector: CARL Source Factory
CARL Source Factory is our solution of CMMS dedicated to the industry sector. It has been designed to guarantee you the best operating conditions for industrial equipment, associated structures and the safety of your personnel. It allows you to manage your maintenance activities in real time, new works and regulatory diagnostics, monitor your service providers and manage your contracts while reconciling quality and budgetary control. Designed in partnership with major industry players, this solution allows you to addressing the challenges of Industry 4.0.